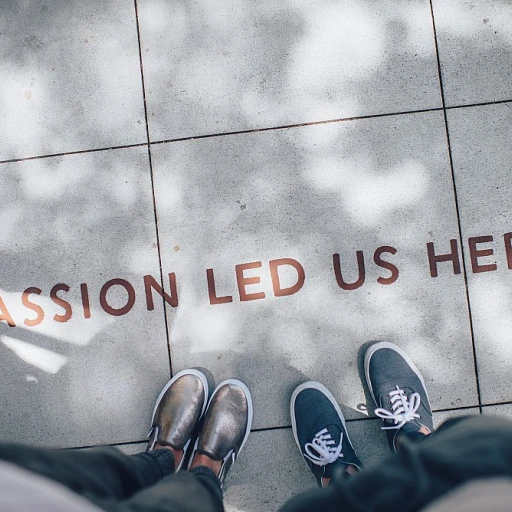
Understanding the Role of Process Improvement in Strategic Management
Importance of Process Improvement in Strategic Management
Process improvement plays a critical role in elevating a company's strategic management. By focusing on enhancing operational efficiency, businesses can dedicate more resources to innovation and customer satisfaction. This alignment not only helps in achieving organizational goals but ensures that continuous improvement becomes a core aspect of business operations. According to a recent study, companies that prioritize process improvement see significant gains in efficiency and productivity. Understanding the fundamentals of process improvement is essential for the c-suite. By identifying inefficiencies within your business processes, you can embark on transformative improvements that lead to sustained competitive advantage. Tools like process mapping and fishbone diagrams offer a visual representation of processes, highlighting areas for improvement. Moreover, utilizing data-driven techniques such as control charts and root analysis provides a nuanced understanding of issues, paving the way for effective problem solving. Integrating quality management principles enables firms to maintain high standards consistently, while lean methodologies help streamline processes to reduce waste. For those in strategic roles, leveraging improvement tools can facilitate better decision making and project management. By understanding the intricacies of these tools within a larger strategic framework, executives can drive initiatives that align with the company's long-term objectives. As noted in a detailed analysis on enhancing organizational efficiency for c-suite executives here, aligning operational processes with strategic goals is key to unlocking new business potential.Identifying Key Process Improvement Tools for the C-Suite
Discovering Essential Tools for Operational Excellence
In the realm of strategic management, leveraging process improvement tools is critical for the C-suite aiming to enhance business operations. As organizations adapt to rapidly evolving market dynamics, identifying the right tools becomes vital. These instruments can empower leaders to make informed decisions, drive quality management, and ensure robust problem-solving frameworks. When selecting tools to improve processes, consider those that aid in thorough analysis and provide actionable insights. Key options include process mapping and stream mapping—to visually represent workflows and identify areas for improvement. Tools like control charts and fishbone diagrams offer a data-driven approach to quality control and root cause analysis, further enhancing problem-solving capabilities. Continuous improvement is the backbone of operational efficiency, and improvement software solutions can play a pivotal role. These platforms help streamline project management, enabling teams to focus on lean methods and reduce waste. A robust improvement software can support continuous monitoring and facilitate regular feedback loops, aiding in sustaining enhancements over time. Implementing effective improvement tools also requires considering the organization's unique needs and objectives. Tools should aid in enhancing customer satisfaction and optimizing business processes without creating additional complexity. Gemba walks, for example, allow leaders to observe processes firsthand, fostering a culture of continuous improvement and informed decision-making. For those seeking insights on integrating such tools within strategic frameworks, unlocking the secrets of operations consulting can be a valuable resource. Understanding how to effectively use these tools can provide your company with a competitive edge, improve work quality, and ultimately drive sustainability and growth in the marketplace.Integrating Process Improvement Tools into Company Culture
Fostering a Culture of Continuous Improvement
Integrating process improvement tools into a company's culture is essential for long-term success and sustained benefits. By embedding these tools in day-to-day operations, businesses can promote a culture that values innovation and quality. One effective way to integrate these tools is by aligning them with the overall business strategy and goals. Connecting process improvement initiatives with strategic objectives ensures that all efforts are geared toward common business outcomes. This helps employees understand the significance of their tasks and how they contribute to the larger mission. Identifying and utilizing the right improvement tools is also crucial. From lean process tools to improvement software, choosing the appropriate tools can streamline business processes and improve efficiency. Gemba walks, for instance, provide insights into actual work conditions, while process mapping helps in visualizing processes and identifying bottlenecks. Integration also requires a data-driven approach. Continuous improvement relies heavily on accurate data and thorough analysis to inform decision-making. Teams must use quality management tools, like control charts, to monitor performance and identify variances that may indicate problems. Additionally, employing root analysis techniques, such as fishbone diagrams, can help pinpoint the underlying causes of issues and drive effective solutions. Encouraging open communication and collaboration amongst teams is vital. By fostering a team-oriented environment where feedback is valued, companies can drive customer satisfaction and enhance quality outcomes. Moreover, regular trainings and workshops can equip employees with the necessary skills to utilize these tools effectively. The integration process is not solely about implementing tools—it’s about transforming mindsets and reinforcing the significance of improvement in every aspect of the business. By focusing on both the technical and cultural aspects, businesses can unlock the full potential of their process improvement initiatives and sustain them in the long run. For insights on enhancing team support for strategic leadership, visit build strategic support.Measuring the Impact of Process Improvement Initiatives
Harnessing Metrics to Gauge Process Improvement Success
Embracing process improvement initiatives demands not just a focus on the implementation but also on evaluating their efficacy. The real value of these upgrades lies in their ability to drive better business outcomes. To achieve this, accurate measurement is essential.- Data-Driven Decision Making: A comprehensive analysis of performance data is critical. Employ data-driven methods to assess how these improvements enhance operational efficiency. Monitoring productivity metrics pre- and post-implementation ensures a tangible impact on business processes. This approach aids in uncovering the quality of process changes over time.
- Tool Utilization: Leveraging quality management and improvement software can significantly aid this measurement. Tools like control charts and fishbone diagrams reveal insights into process efficiencies and help identify potential problems. These resources shine a light on lean techniques, fortifying the path towards continuous improvement.
- Customer Satisfaction Levels: An often overlooked, yet pivotal aspect, is customer feedback. These voices are invaluable in gauging how process changes resonate externally. Positive shifts in customer satisfaction can be a robust indicator of successful process improvements, leading to better business outcomes.
Overcoming Challenges in Process Improvement Implementation
Addressing Common Hurdles in Process Improvement
Implementing process improvement strategies can be a daunting task for any organization. The journey towards enhanced operational efficiency is often fraught with challenges that require careful navigation. Understanding these hurdles and devising effective solutions is crucial for the C-suite aiming to drive meaningful change.
Resistance to Change
One of the most significant obstacles is resistance from employees. When new improvement tools and processes are introduced, it's common for staff to feel threatened or overwhelmed. This resistance can stem from a lack of understanding or fear of the unknown. To mitigate this, leaders must prioritize clear communication and provide comprehensive training that highlights the benefits of new systems. Encouraging a culture of continuous improvement can help ease transitions and foster acceptance.
Complexity of Tools and Processes
Another challenge is the complexity of the tools themselves. Whether it's process mapping, lean management techniques, or improvement software, the tools can be intricate and require a steep learning curve. To overcome this, organizations should invest in user-friendly solutions and provide ongoing support to employees. Simplifying the tools and making them accessible can significantly improve the adoption rate and effectiveness of process improvement initiatives.
Data Management and Analysis
Effective process improvement relies heavily on data-driven decision making. However, managing and analyzing vast amounts of data can be overwhelming. Implementing robust data management systems and employing skilled analysts can help organizations harness the power of data. By doing so, companies can identify problems more efficiently and develop targeted solutions that enhance customer satisfaction and business performance.
Maintaining Momentum
Once initial improvements are made, maintaining momentum can be challenging. Continuous improvement requires ongoing effort and commitment from all levels of the organization. Establishing a dedicated team to monitor progress and ensure adherence to new processes is vital. Regular gemba walks and control charts can help leaders stay informed and engaged, ensuring that improvements are sustained over time.
Conclusion
Overcoming these challenges is essential for successful process improvement implementation. By addressing resistance, simplifying tools, managing data effectively, and maintaining momentum, organizations can achieve significant gains in operational efficiency. The journey may be complex, but with the right strategies and commitment, the C-suite can lead their organizations to new heights of success.
Case Studies: Successful Process Improvement in Action
Insightful Applications of Process Improvement in Action
Analyzing successful real-life cases of process improvement provides valuable insights into how these transformative practices can be effectively implemented across different organizational landscapes. Here we explore how diverse companies have harnessed improvement software, data-driven approaches, and quality management tools to elevate their business processes.1. Efficient Supply Chain Revamp
Companies facing supply chain disruptions have turned to lean methodologies and root analysis to streamline their operations. By employing process mapping and improvement tools like the fishbone diagram, businesses succeeded in identifying bottlenecks and inefficiencies. This led to enhanced process control and timely delivery, boosting customer satisfaction and cornering the market on reliability.2. Boosting Quality in Manufacturing
A prominent manufacturer leveraged continuous improvement strategies and quality management tools to elevate their production processes. Employing control charts for real-time monitoring, coupled with regular Gemba walks to identify on-the-ground challenges, they achieved a marked improvement in product quality. Customer satisfaction ratings climbed as defects decreased significantly.3. Customer Service Excellence
In a competitive service industry, a focus on data-driven decision making and problem-solving tools helped enhance the customer experience. Businesses employed process mapping alongside improvement software to streamline customer interactions and service delivery. As a result, they reported a significant reduction in resolution times and a noticeable increase in customer loyalty. These case studies set a precedent for integrating robust process improvement tools within strategic management. They demonstrate how thoughtful analysis and adaptation can lead to substantial organizational gains and underline the importance of continual assessment in overcoming operational challenges.